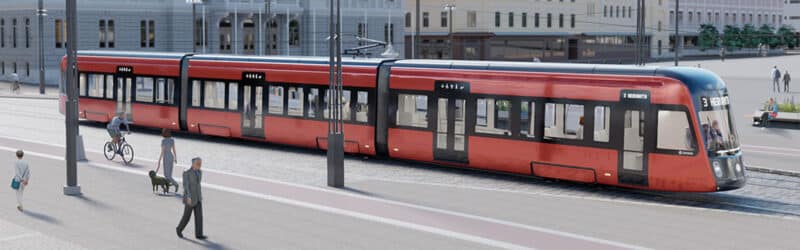
A tram designed based on end-user feedback
This article may contain outdated information.
Transtech’s first rolling stock project with a full maintenance service contract
Tampere Tram starts to operate officially in August 2021, but trial traffic with passengers began already in May 2021. The project’s rolling stock supplier Škoda Transtech Ltd’s plant in Kajaani, Finland manufactures 20 trams for the Tampere light rail system, as well as is responsible for their maintenance and upkeep. The project began behind schedule, but it will finish on schedule. Moreover, Tampere has been delivered with trams full of new technology and comfort for both tram drivers and passengers.
A new type of project to the parent company
Mr Ville Marjamaa, who is responsible for the design part of the project at Transtech, states that the deliverable does not actually differ from the company’s core rolling stock business. For example, the delivery batch size is 20 trams. Typically, the batch size in similar projects varies from 15 to 40. Moreover, the contract includes maintenance of the vehicles for 10 years, or optionally for the vehicles’ entire life cycle.
Although the batch size is typical to Transtech, the final product is a completely new addition to the company’s product portfolio. Transtech had already begun designing a five-module, bidirectional tram for the Helsinki Jokeri Light Rail project when the Tampere Tram project began. However, the two trams had to meet different requirements, making the final products different from one another.
“For all intents and purposes, we can consider the Tampere tram to be a completely new product. It is ten metres longer and 25 centimetres wider than usual, which caused challenges to the strength and mechanical design of the body.”
“Moreover, the track gauge is almost 50 centimetres wider than usual, which required the design of a completely new bogie. The bogie is the key part of a tram around which the motion characteristics of the tram are built. The trams also had to be bidirectional with entrances on both sides of the car, which raised the difficulty level for their design even more”, highlights Marjamaa.
The Tampere project was a first of its kind also to the parent company, which had not yet designed a bidirectional tram, which can be controlled from driver cabins at both ends of the tram, and which has entrances on both sides of the car.
Many systems in a tight space
According to Mr Marjamaa, the three of the most difficult parts of a rolling stock project are space, weight and schedule. This is because the passenger compartments must be as spacious as possible, but the total size of the tram should be as small as possible. Typically, when the passenger compartments are spacious and comfortable to use, there is little space left for technology and electromechanical equipment behind the interior panels and under the floor.
“As the technical requirements became more precise as the project moved further, we had to figure out how to include all combinations and details, while making everything work properly. Moreover, everything had to be duplicated because each function has to be controllable from both driver cabins. As a result, each function has been built so that it can be controlled from the chosen driver cabin. However, there was no existing solution available that could have been used as a starting point.”
The Tampere Tram conceals inside a dozen systems requiring separate specifications, such as air conditioning, main and support operating systems as well as door, sanding, wheel flange lubrication and passenger information systems, which include screens and cameras, audio systems and the driver’s displays. In addition, the tram cars conceal inside 10,000 coupling points and over 20 kilometres of cable.
With these systems, the trams are connected to time. The information generating systems already share some information with the driver and maintenance about the current state of the cars, the users and the condition of the rolling stock, but in the future even more information can be generated.
“Operative diagnostics tells us how the tram is working. In the future, a video headcount system will be added, as well as other systems to tract maintenance requirements.”
“It is important to be able to track maintenance requirements in real time. It is also important to recognise when maintenance is not required.”
E3 software as the basis of electrical design
In this project, Comatec was responsible for the tram’s electrical and electromechanical design and placement, wire modelling and component mounting. At best, 10 people from Comatec’s electrical design team in Tampere and four from Comatec Poland took part in the project.
“From the design engineer’s point of view, the biggest challenge in the electromechanical design has been the fitting of components and cables to the given space. There is so much cable that hiding all of it was no mean feat for our design engineers”, explains Business Unit Manager Janne Hirvonen, who led the electromechanics and system design part of the project at Comatec.